Can spare parts fit in your pocket?
During wartime, faulty materiel must be replaced quickly. It is crucial for all military operations to maintain control over the supply chain. The battle may be lost if it takes too long to obtain spare parts. Ideally, production in the field would replace defective parts. This is why 3D printing is currently being studied in detail by FFI.
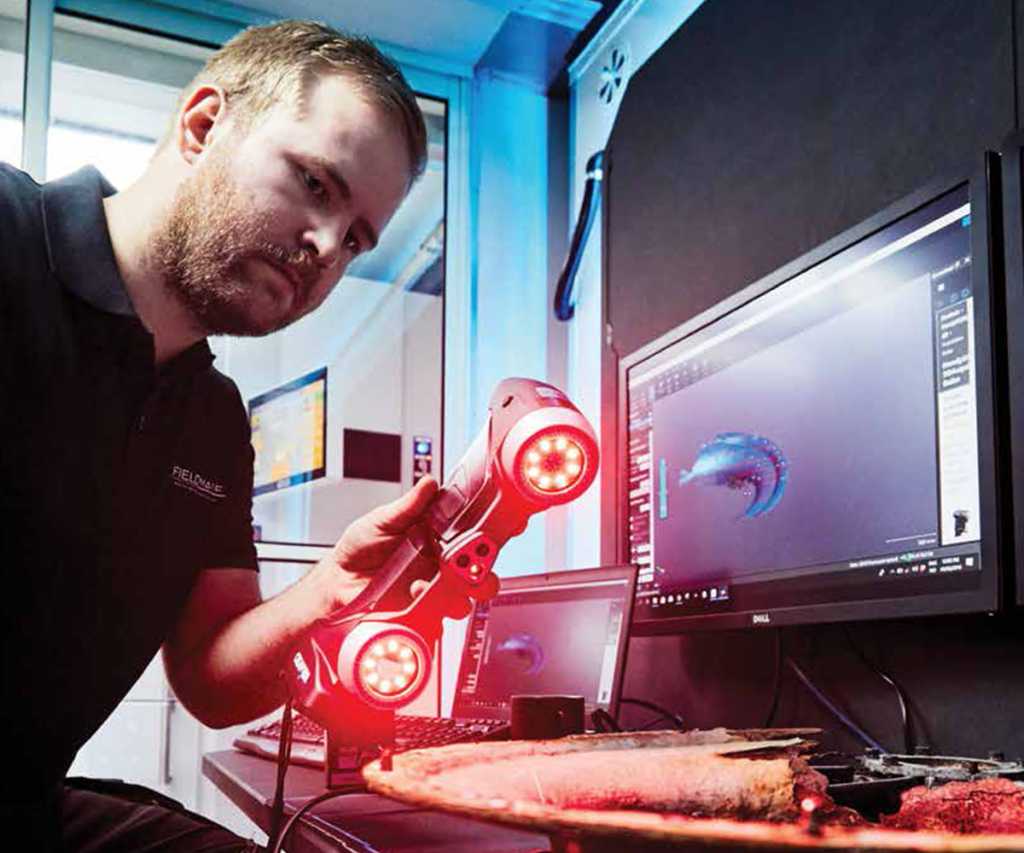
For FFI and the Norwegian Armed Forces, 3D printing is about keeping up with technological developments. It is essential to look at the types of use that may arise. FFI’s Product Development, Testing and Verification (PTV) is where these methods can be examined.
Rapid, local production would require a new type of logistics. In this case, it would be possible to avoid larger storage of spare parts. Components can be replaced immediately. FFI is collaborating with the Norwegian Armed Forces and suppliers to learn how this would work in practice.
Factory quality
Production of a spare part using 3D printing can take anything from a few hours to a day or two, depending on size and material. Technically, it is possible to use polymers or various types of metals, such as aluminium, titanium and stainless steel. It is also easy to produce soft parts, such as gaskets.
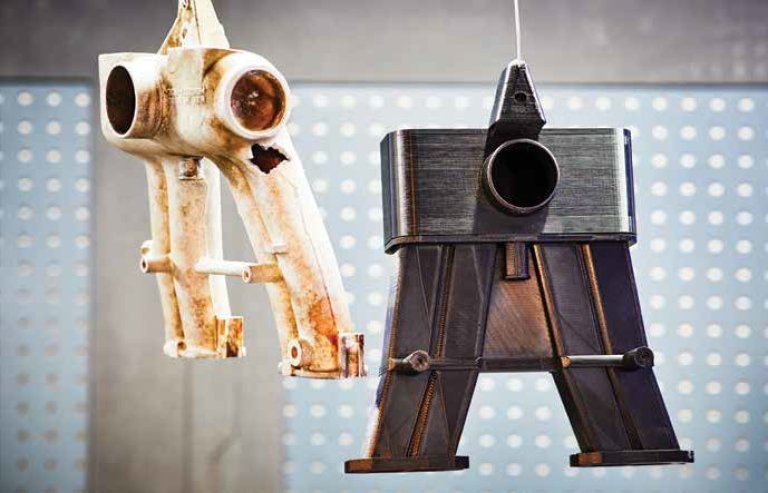
These products are just as good as those from traditional factories, and the quality is identical. Our vision is that these microfactories will become so good that they render large storage units superfluous. ‘Local’ is the key word for spare parts for future defence materials. For Christian Duun Norberg, this was the beginning of something big. With the Fieldmade company, the former officer’s goal is to change the digital ecology for everyone who currently requires large storage units and demanding logistics. Not only for the Norwegian Armed Forces, but also for larger companies, such as Equinor.
Physical storage requires space and localisation, perhaps far away from those who need the delivery.
"The oil industry also requires solutions that can increase operational capability and level of preparedness. We can offer on-site production laboratories. Basically, we are able to digitalise clients’ spare parts storage. By extension, we can stop talking about ‘spare parts’. In a sense, you have your spare parts in your pocket, wherever you are".
A special container
Top US military personnel showed a strong interest in one special personnel container during the 2018 NATO exercise Trident Juncture. Inside of the container, called Nomad, they were able to see how Fieldmade produced exact copies of damaged materiel. With high quality and in a short amount of time.
"Obtaining spare parts can take several days. Here, a damaged component can be 3D scanned. Missing pieces of the object are recreated. Alternatively, the component can be produced from the same data file as the original. Those who need the part can come and pick it up the next day", says Norberg.
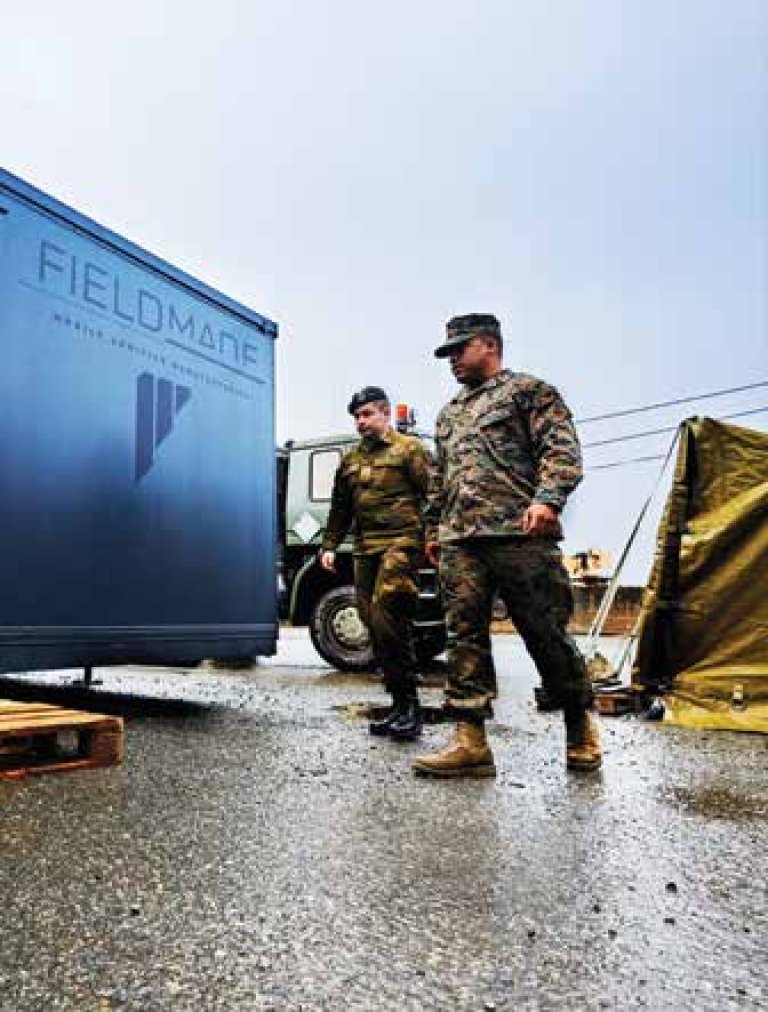
The NTNU graduate and naval special operations commander states as follows:
"During the NATO exercise, we demonstrated the two most important reasons why 3D printing is here to stay: Essential components can be delivered quickly and require less storage. Remember: Physical storage requires space and localisation, perhaps far away from those who need the delivery. Digital storage requires neither of these things".
Fieldmade does not view the company as a microfactory. The future can be bigger than that. Fieldmade is an early representative for what is referred to as additive manufacturing (AM). "This industry will have an enormous impact on the military supply chain and its operations. This is the near future", says Norberg. So far, there has been little discussion about additive manufacturing factories for defence purposes. But this is now snowballing.
FFI is at the forefront of this technology in Norway. This is why the institute has also established cooperation with academia and research institutions, both nationally and internationally.
FFI wants spin-off industries
Fieldmade is the type of spin-off industry that FFI wants. The company was established at Kjeller. The researchers who participated were among the driving forces. They contributed by sending a project application to the Norwegian Research Council. During this phase, the name Fieldmade was proposed. This is a name that literally describes what it does. PTV at FFI was also key. Christian Duun Norberg recruited people from this group to continue with the work. "It was essential to collaborate with FFI.
Here, I found people with the same interests. Thus, it became an exciting place to work. We were a team of three or four people who volunteered to work on this idea in addition to our actual assigned projects. In a sense, we were educating ourselves. This work materialised into something that would otherwise have simply remained a good idea. Suddenly there were seven of us and the idea became a separate project", says Norberg.
He has no doubts about future prospects. They are bright.
"I have noticed a stronger interest in something that previously was not well understood. The world needs time to mature. The Norwegian Armed Forces has to see the potential. The defence industry is profiting from solutions that are available today. Now we can collaborate on moving forward".