This is the story of how a battery, a good idea and a cup of coffee became a Norway industrial fairy tale.
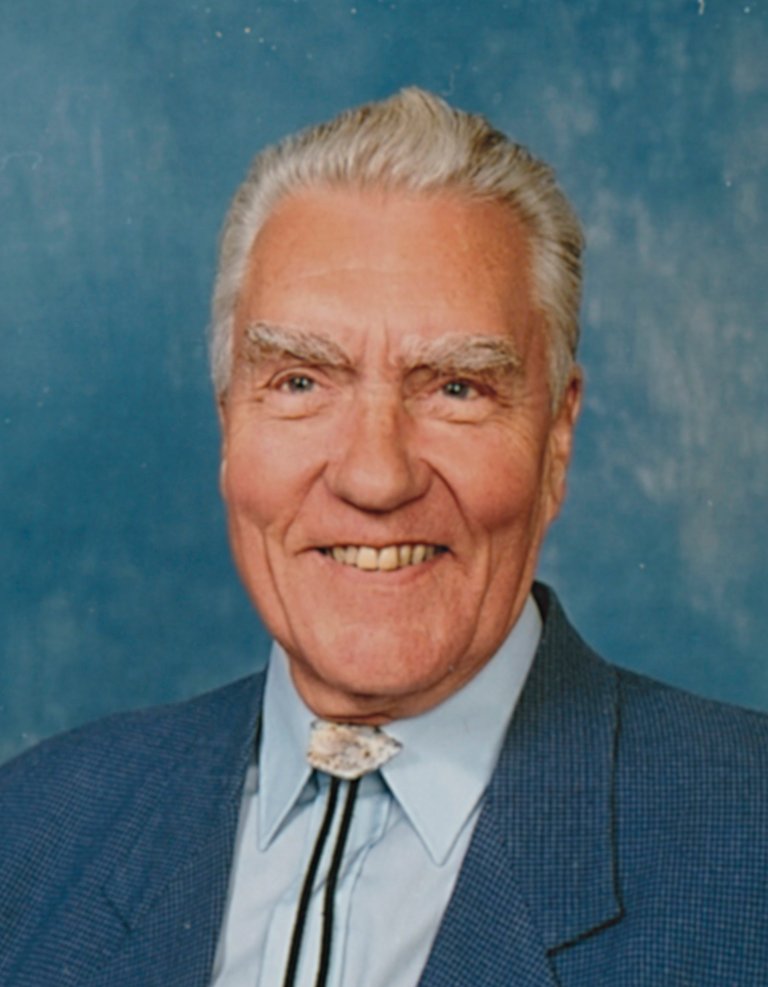
One day in 1993, a man in a grey suit and bolo tie, with bushy eyebrows and finely combed slicked-back hair, approaches Statoil Director Martin Sigmundstad at Fornebu and offers him a hot cup of coffee.
Without this cup of coffee, and the chat that followed, one of FFI’s greatest achievements would perhaps never have seen the light of day.
The man with the distinct eyebrows is named Per Thoresen and is a Research Director at FFI. Since the 1970s, he has had the idea to use batteries to power small, unmanned submarines.
The Norwegian Armed Forces was sceptical
At this time, in the early 1990s, there are already a number of small submarines in use, but these receive power and control signals via a cable that runs to a ship on the surface. Can a submarine be created that operates independently in the deep sea? That can map the seafloor, search for mines, conduct espionage or warfare entirely on its own or remotely operated from a ship?
This idea has been difficult to sell, both with management at FFI and in the Norwegian Armed Forces. However, by the late 1980s, battery technology has become so advanced that it is possible to try. Three years earlier, Thoresen has managed to convince the Intelligence Staff at the Norwegian High Command to grant funds to make an attempt.
FFI researchers have created a new saltwater battery that can power a mini submarine for 1200 nautical miles – i.e., from Oslo to Alta. With the funds from the Intelligence Staff, they develop AUV Demo (Autonomous Underwater Vehicle) – a shiny yellow test submarine, and a system to transmit control commands down to the submarine using acoustic communication (noise signals).
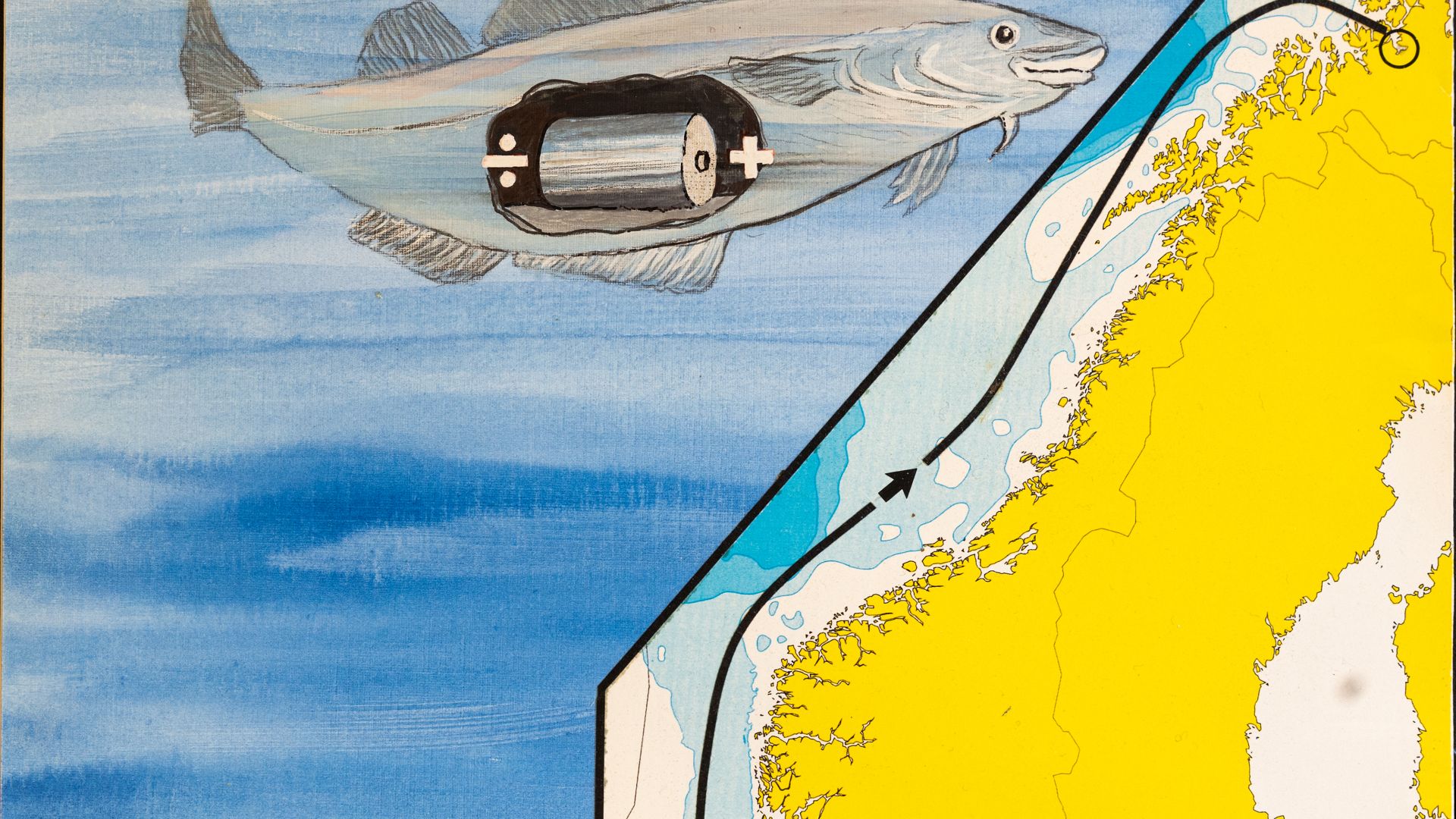
Battery-powered cod?
This is how FFI’s design office presents the new battery technology in the early 90s – as a battery-powered cod that can swim from Oslo to Alta.
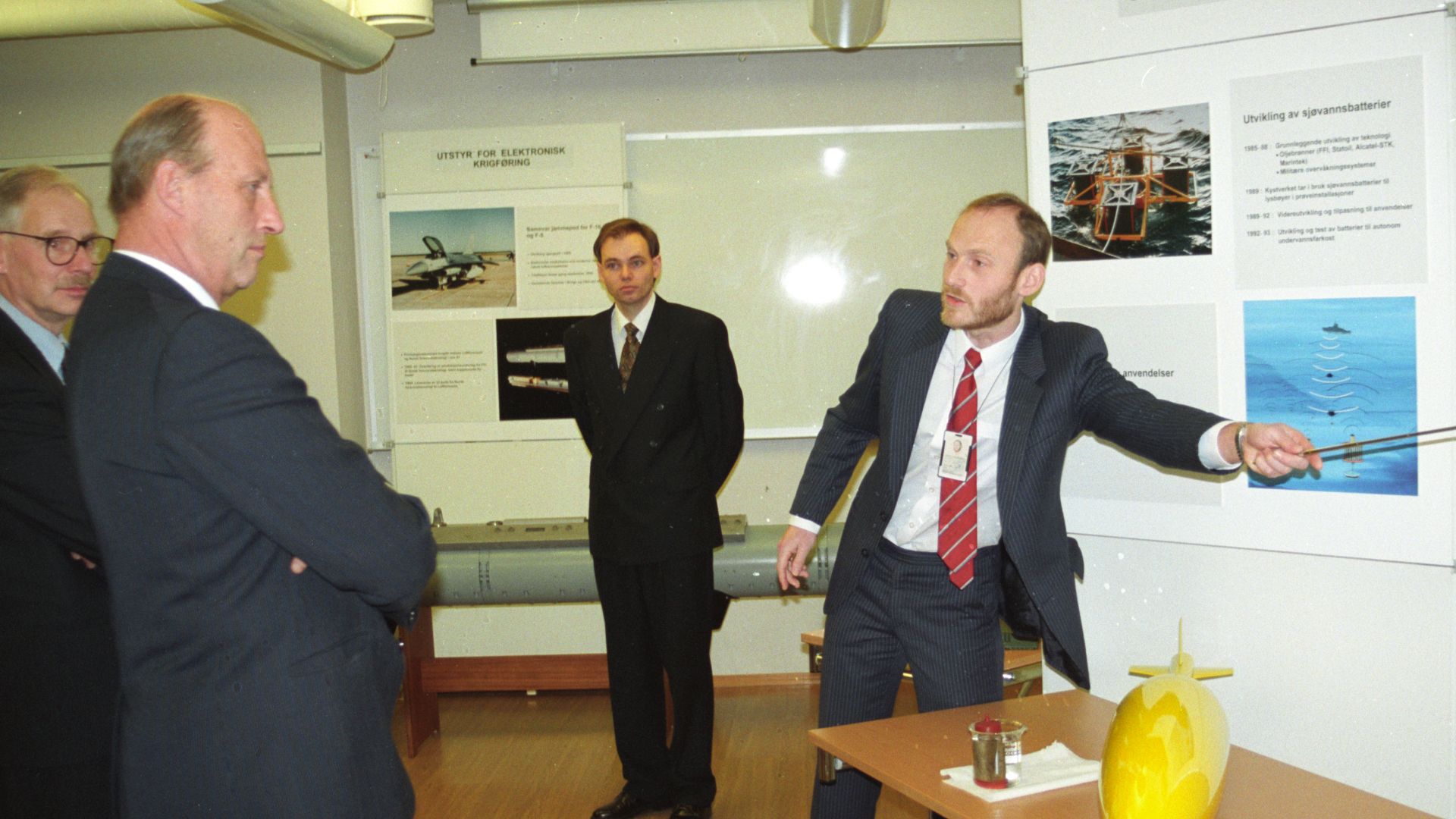
King Harald V visits FFI in 1994. Research Director Nils Størkersen describes FFI’s plans for an autonomous underwater vehicle. The purpose of such a submarine for the Norwegian Armed Forces is still not entirely clear.
Had to swim without a tether
The very first miniature model from Bøletjern is today sitting in Nils Størkersen’s office. He has been the project manager for the development of Hugin and has followed the submarine from the idea stage to a finished commercial product.
The battery FFI used in AUV Demo was a seawater battery. As the word suggests, it uses seawater as the oxidizing agent.
“We needed 20 litres of seawater to pass through the battery every second in order for it to produce enough power to propel the vehicle through the water. This meant we couldn’t have a tether fastened to the submarine. A tether would have slowed down the submarine so much that the concept wouldn’t have worked”, says Størkersen.
Simply put, the new vehicle needed to be tetherless.
During a demonstration in May 1993, AUV Demo swims 109 nautical miles in Skagerrak with only “a few mishaps”, as it is stated in the report at the time.
Despite a successful demonstration – the funding stops after this. The Norwegian Armed Forces has reservations about spending more money on development. And it is still a long way to go until such a submarine is fully developed and ready to be manufactured and purchased by the Norwegian Armed Forces.
In deep water
Since the funding from the Norwegian Armed Forces has stopped, FFI needs a new cooperation partner. Thoresen and Størkersen look to the offshore industry.
It turns out that the cup of coffee FFI offers Statoil in 1993, is a very well-timed cup.
Oil exploration has just been permitted on the Vøring Plateau in the sea outside Nordland County. Here, the seafloor is up to 1500 metres below sea level. There is a shortage of the technology used to map deep sea areas with the quality and effectiveness required by the offshore industry.
“Mapping was a cost driver, involving large ships and crews. If we were to contribute to mapping an area in half the time, this would provide Statoil with a good argument for supporting our technology”, says Størkersen.
At the time, the environment and the companies involved in seafloor mapping were sceptical. They used what is referred to as ‘Remotely operated underwater vehicles’ (ROVs), where communication with the surface and power supply are provided via a cable.
“At great depths, the cable is so long that it becomes difficult to maintain an acceptable speed through the water. They probably viewed the AUV technology as a threat”, Størkersen recalls.
He says they “downplayed” the technology to overcome the scepticism.
“We had to be conscious of how we described it. We didn’t sell it as an autonomous submarine. We sold it as an untethered, remotely operated submarine. “It’s a virtual tether”, we said.
A napkin at an airport
With Statoil on board, development gained speed.
Statoil, FFI and Simrad (Kongberg Maritime) now commenced a project to develop an untethered underwater vehicle for detailed, deep-sea seafloor mapping. It was given the name: HUGIN (High-precision Untethered Geosurvey and INspection system).
The project is funded by Statoil. Simrad (Kongsberg Simrad from 1997, now known as Kongsberg Maritime) is the envisaged manufacturer. FFI has the main responsibility for the development. Nils Størkersen from FFI heads the development project.
The old seawater battery from AUV Demo is not effective enough to power an AUV for seafloor mapping purposes. Therefore, a new battery concept is developed.
This was before the lithium-ion batteries that are used in modern electric cars and electronic gadgets. How to create a battery with enough power and lifespan to operate a tetherless submarine with advanced sensors and computing power?
The solution to the battery problem arrived when Øystein Hasvold and Nils Størkersen were doodling at an airport in the United States. They got the idea to combine the technology of a seawater battery with the technology from another battery that FFI was developing for use on land.
“Hasvold was an incredibly creative and versatile researcher. He was the source of the battery concepts from FFI and also contributed significantly to the hydrodynamic design and system architecture of the vehicle. What he envisaged usually worked when we tested, calculated and verified”, says Størkersen.
The initial draft of the ‘aluminium-hydrogen peroxide’ battery which the two researches jotted down at an airport in the United States was patented and industrialised and was in use in Hugin all the way until 2008. However, by the early 2000s, the battery technology had caught up with FFI’s patents. Subsequently, all new Hugin submarines were equipped with lithium-ion batteries.
The breakthrough
In the period from 1995, there were some intense years during which researchers and engineers worked on developing a control system, navigation and software to process sonar data. They also had to design a system to launch and recover Hugin from vessels.
This was a major undertaking. The quality requirements were strict. The end product had to work in deep water and produce topographical seafloor maps with a resolution of one metre. Furthermore, it needed to operate in real offshore conditions on the Norwegian continental shelf.
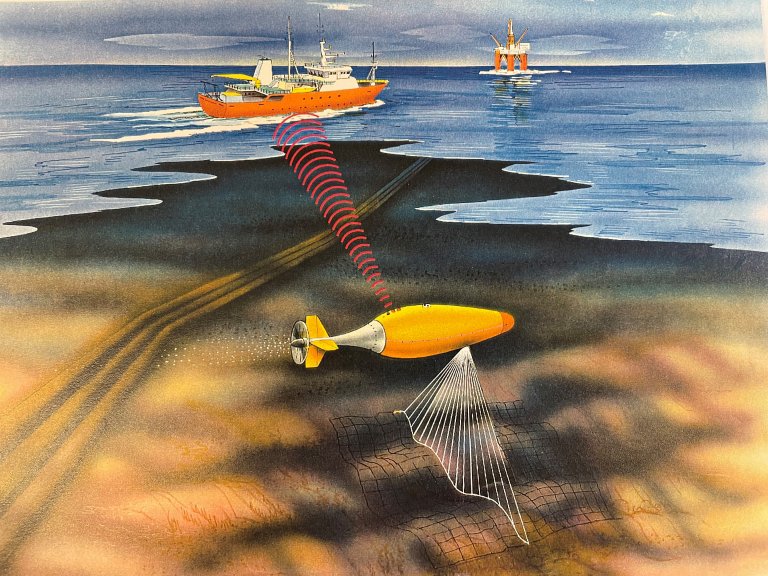
Kongsberg Simrad (Kongsberg Maritime) was responsible for all electronics, cabling, power systems, acoustic positioning, communication and sensors, and they provided considerable input and funding to the project. FFI was responsible for the actual vehicle and the launching/recovery system, and for software for navigation and control system.
“The Hugin Project shows how well it is possible to cooperate across departments and between various enterprises if the conditions are facilitated and everyone has a common objective”, says Størkersen.
Thanks to the Hugin Project, FFI developed a world class navigation environment. NavP – the navigation programme that was developed in order for Hugin to be able to understand where it is underwater, is currently in use in a number of products and underwater vehicles.
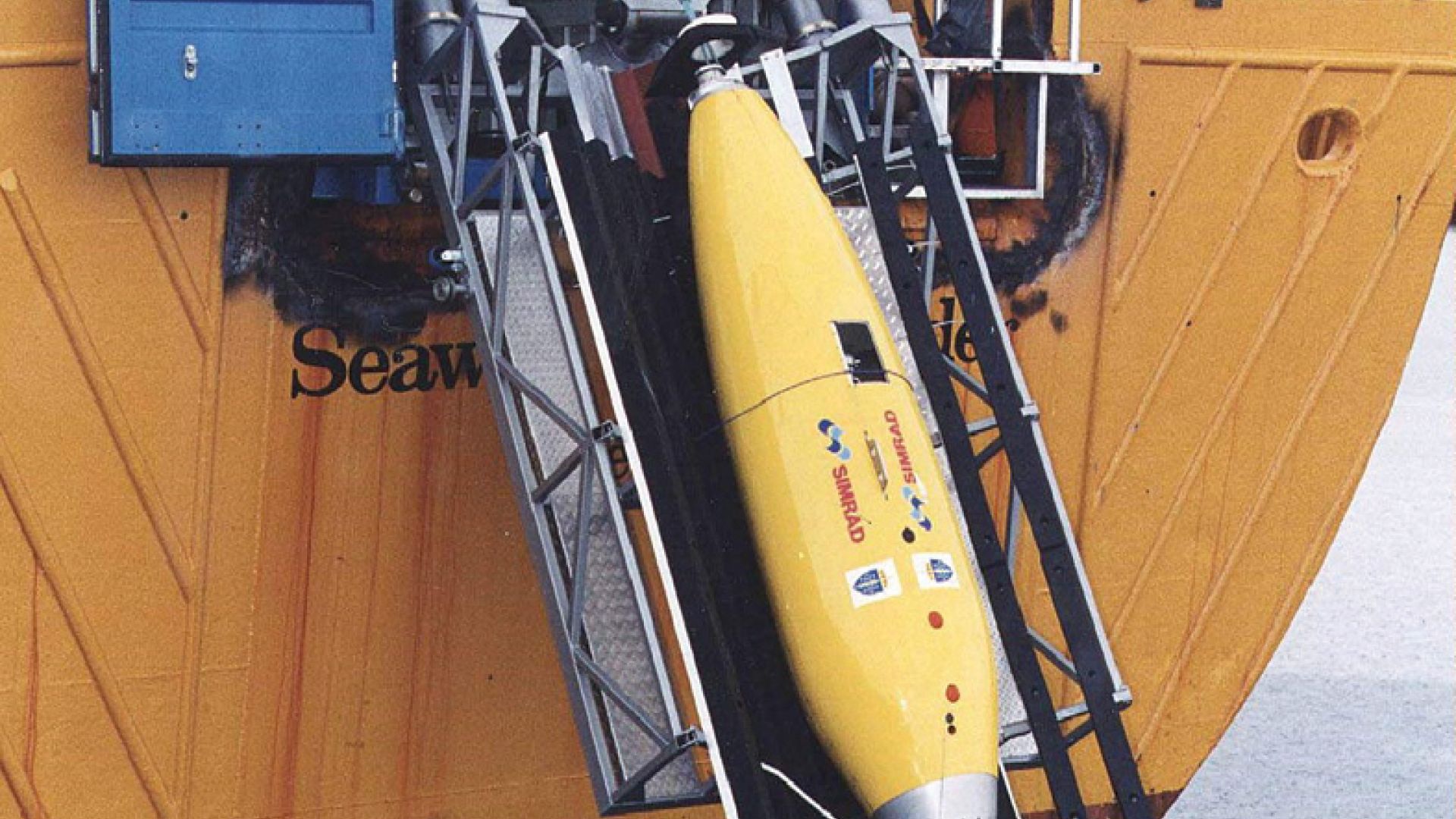
In 1997, Statoil organised an operation to see how well Hugin could map the seafloor compared to a traditional survey submarine controlled from an operator ship via a cable (ROV). The analysis was performed by the survey services company Stolt Comex Seaways AS.
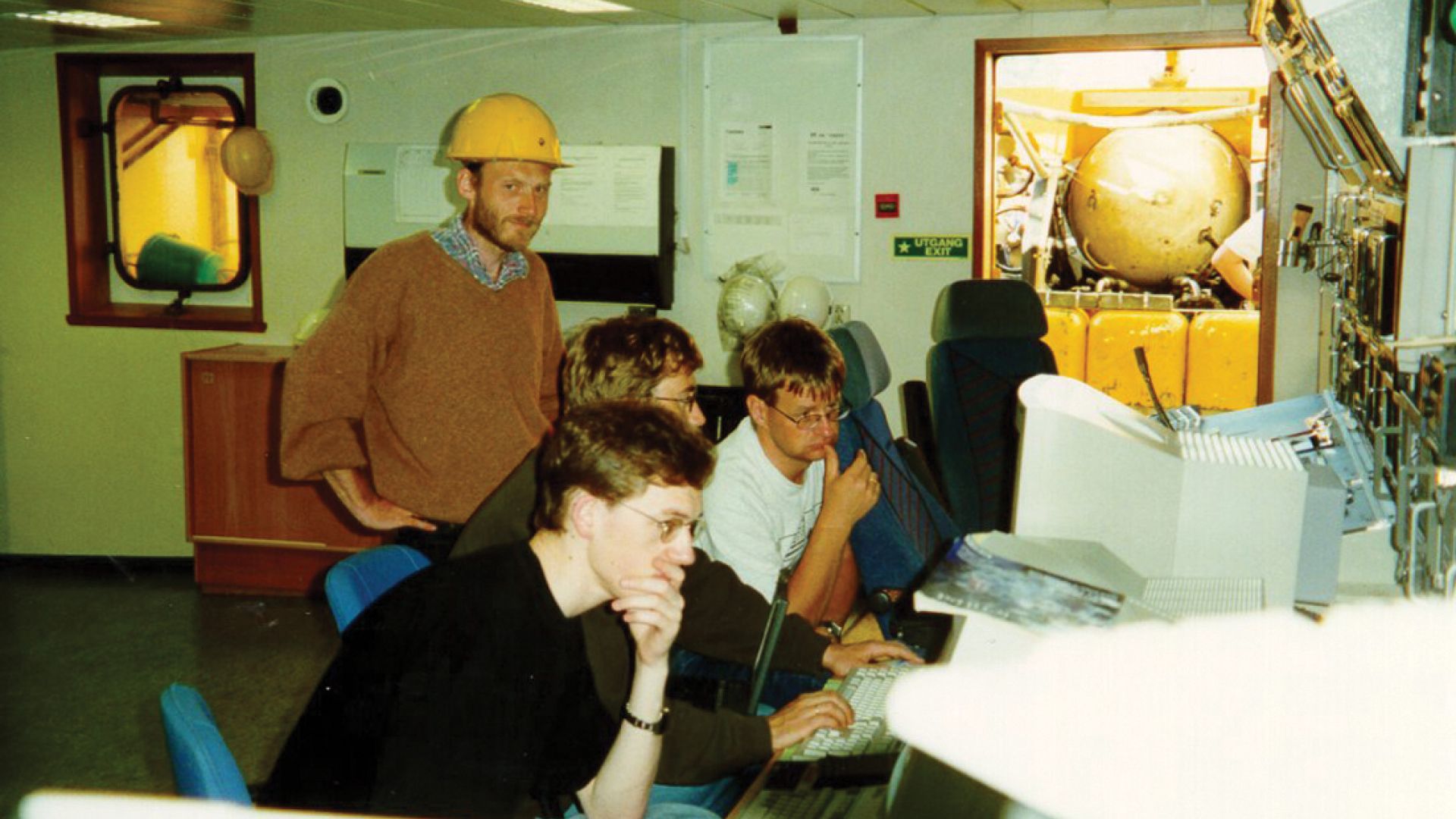
What followed were five intense days with minimal sleep for the Hugin team. Here, Morten Kloster, Bjørn Jalving and Jon Kristensen are working in front of the computer monitors. In the background is Nils Størkersen.
The work paid off: Hugin mapped the seafloor faster and with as good quality as the ROV.
In 1999, Kongsberg Simrad succeeded in winning a contract for the sale of a HUGIN vehicle to the U.S. survey services company C&C Technologies. Thus, the international breakthrough was a fact. The vehicle completed a planned three-year mapping undertaking in the Gulf of Mexico in just eight months.
Since then, Kongsberg Maritime has sold a number of HUGIN vehicles to international survey services companies. In 2018, six Hugin submarines were used in the search for Malaysia Airlines Flight MH370, which disappeared en route from Kuala Lumpur to Beijing with 239 people on board in March 2014.
In 2017, the Norwegian ship “Seabed Constructor”, which is equipped with five Hugin submarines, was able to locate the sunken Argentinian submarine ARA “San Juan” at a depth of 800 metres.
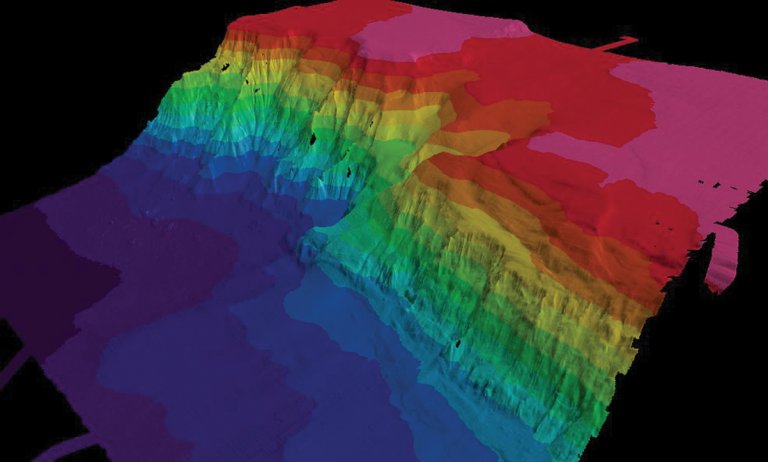
In parallel with the developments for the offshore and oil industry, FFI continued working on the next generation of Hugin that could be used for military purposes.
“The knowledge of future military needs was always in the back of our minds when the civil systems were being developed”, explains Størkersen.
A “genuinely” autonomous vehicle needs to know where it is, where it is going and what it is tasked with doing. In order for the Norwegian Armed Forces to be able to utilise Hugin, it was necessary to develop even better navigation systems and better algorithms so that Hugin could act independently based on what it saw and found on the seafloor.
Exam day
On a cold winter day in 2001, Hugin was finally going show what it was capable of in a defence context.
The project MINEKART was going to be concluded with a demonstration. A launch and recovery system was borrowed from Simrad and mounted on the minehunter vessel KNM Karmøy. A provisional installation for underwater acoustic links and positioning was retrieved from a warehouse at Haakonsvern and fastened to the minehunter just before the demonstration.
6 December 2001
The moment of truth. For the first time, Hugin will show the top brass of the Norwegian Navy that it can detect mines on the seafloor all on its own.
The submarine is released and sends live data back to the minehunter.
The guests then go for lunch, while Hugin continues on its own.
After lunch, Hugin is recovered and the data are downloaded. Hugin has automatically found the four mine dummies that had been deployed in advance.
The demonstration convinces the chiefs of the Norwegian Navy. A few months later, they decide to upgrade KNM Karmøy for Hugin runs. A new project to develop a Hugin adapted to minehunting is commenced.
In 2017, the Norwegian Armed Forces purchased four Hugin vehicles from Kongsberg for a total of NOK 155 million. By 2028, a new unmanned system for detection of naval mines and minehunting will be introduced in the Norwegian Navy.
FFI and Kongsberg are cooperating on the development of this system, as well. The project is now the engine for further development of Hugin.
In this system, Hugin will map the seafloor, while autonomous unmanned surface vessels drag the minesweepers. The operations will be controlled by a manned vessel at a safe distance.
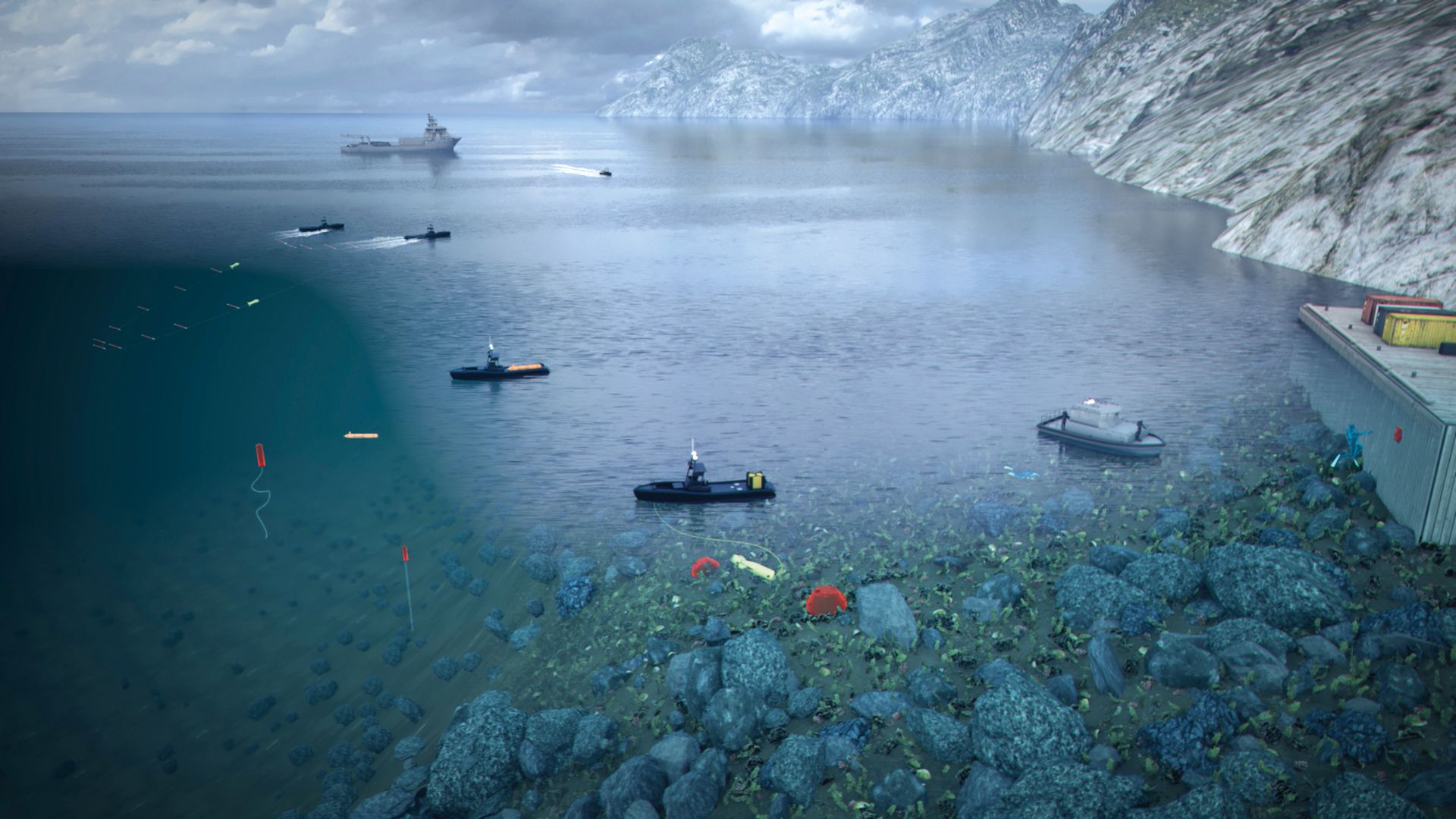
Safer, faster and better
In the new Norwegian system for mine countermeasures, minesweeping, mapping and neutralising are done using autonomous or remotely operated machines. The operations will be controlled by a manned vessel at a safe distance.
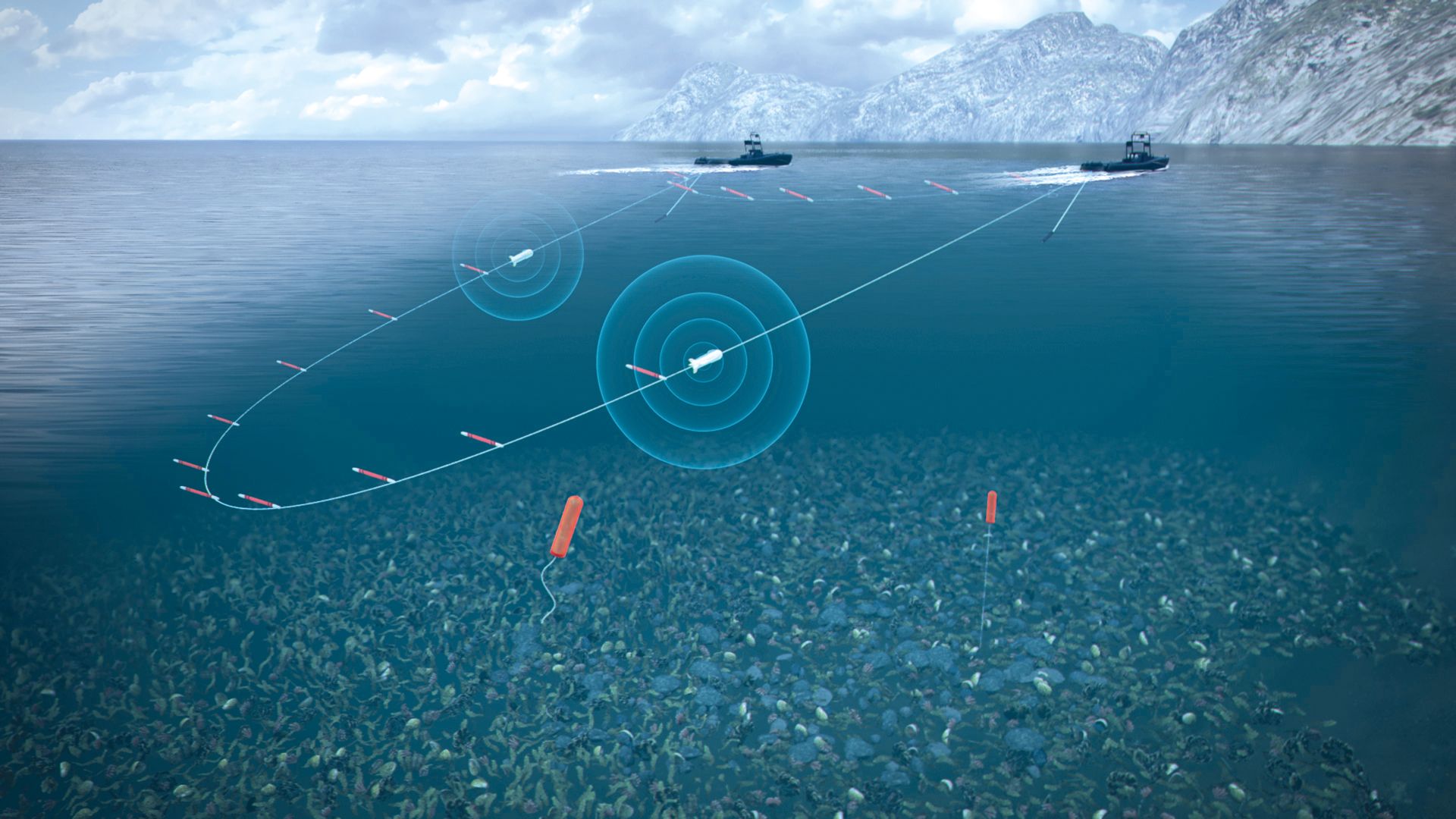
1. Minesweeping
Two unmanned boats pull a sweep between them. This is done to simulate a passing ship and trigger the detonation of the mines.
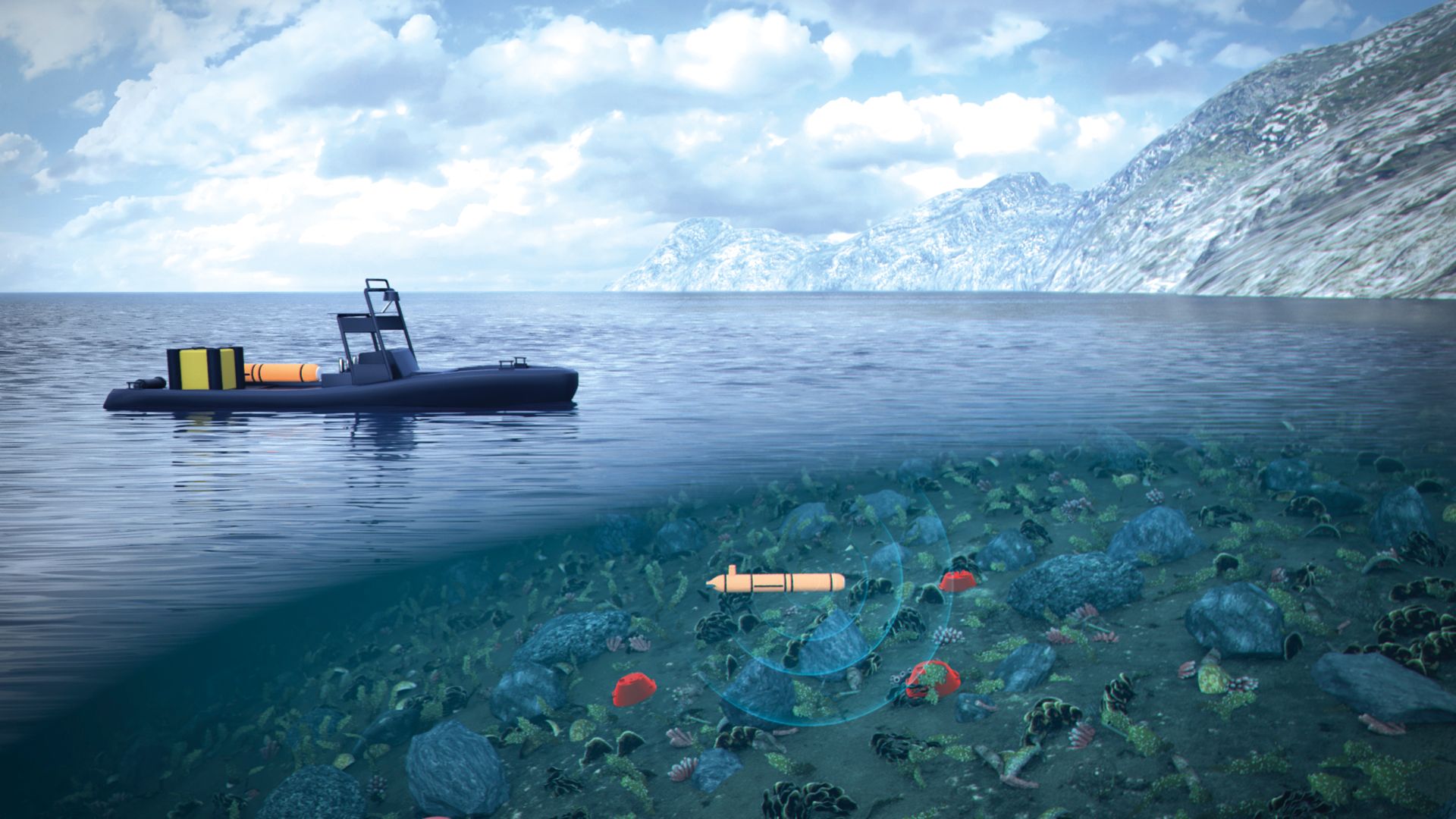
2. Area mapping
Hugin is sent to autonomously map the seafloor in an area. Image recognition algorithms allow Hugin to find mine-like objects on the seafloor, which it examines in more detail. It then notifies the mother ship of where the mines are located and what kinds of mines they are.
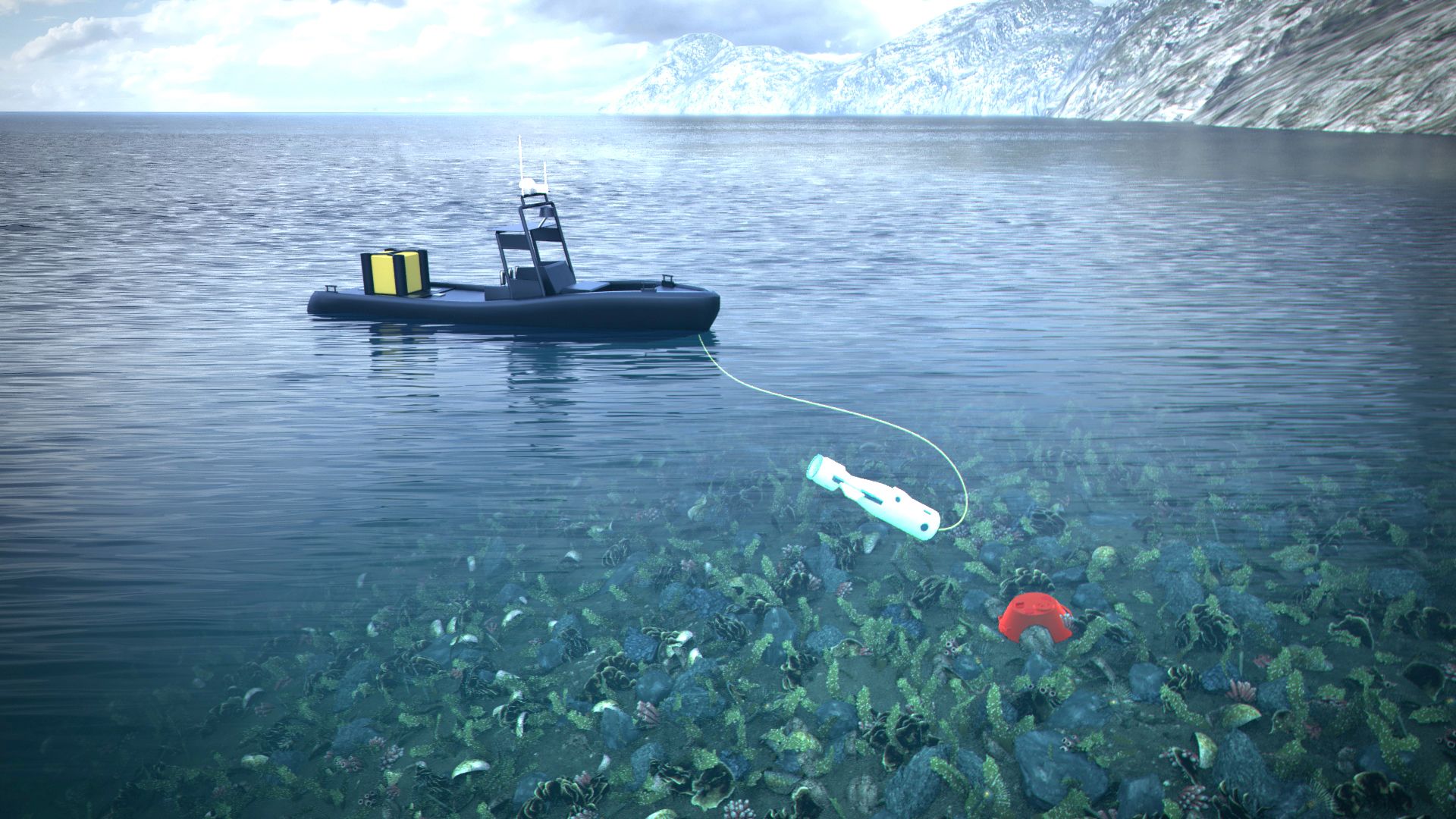
3. Neutralising
An unmanned boat is deployed with a single-use weapon to neutralise the mines. The single-use weapon is connected to the unmanned boat using an optical cable. An operator on the mother ship controls and fires the weapon. In complex situations, mine clearance divers have to be deployed to solve the problem.
Belief in cooperation
Størkersen currently works as Research Director at the Department of Innovation and Industrial Development at FFI. He has 40 years of experience under his belt from the development of Hugin and other systems.
He believes it is essential that a research institute like FFI cooperates closely with industry partners.
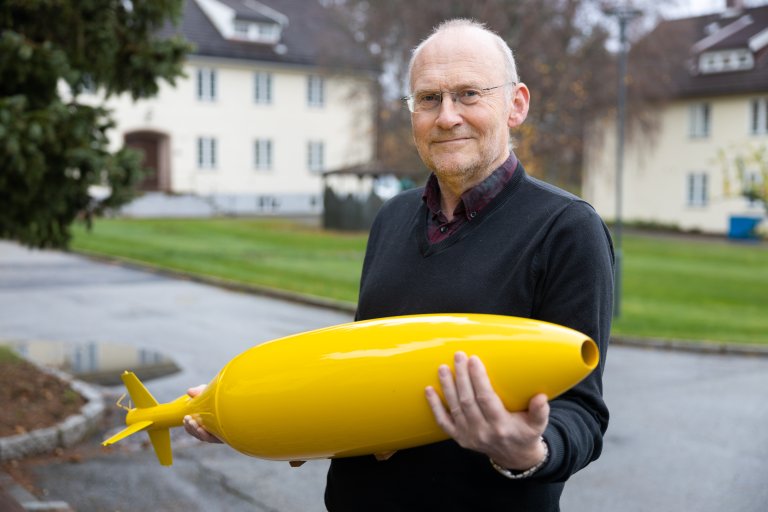
“Innovation is not innovation until it is utilised – i.e., the results from the research and development are put to use by the Norwegian Armed Forces. This is often the most difficult part of the innovation chain. Therefore, FFI’s work is not complete until we have achieved a product that the Armed Forces can use”, says Størkersen.
Hugin is just one of many examples of projects in danger of stopping due to a lack of interest from the Norwegian Armed Forces – whether it is due to high risk, uncertainty relating to cost-benefit, or because the technology has not been mature enough.
“With Hugin, we found a civil application and a partner that could take the necessary risk and open the industrial market for the technology. This contributed to developing the technology to a maturity level that enabled military applications”, says Størkersen.
Will FFI to a greater extent have to find civil cooperation partners in order to develop the technologies the Norwegian Armed Forces needs?
“I think it is likely that this will increasingly be the case going forward. Today’s disruptive inventions largely derive from the civil sector. This has to do with the dynamics in civil industries. Civil industries deliver their products to enterprises or to individual consumers, whereas the defence industry delivers to states. Civil products are therefore sold continuously and in large quantities to highly diverse users and therefore have to be adapted faster to how the consumer market responds to the innovations. Thereby, civil products achieve a more rapid evolution and development rate than military products”, Størkersen concludes.
Are you proud of what you achieved with Hugin?
“Yes. It’s important to work on something that matters. It’s important to do something useful – to leave something behind. But the driving force has mainly been that it’s been fun.
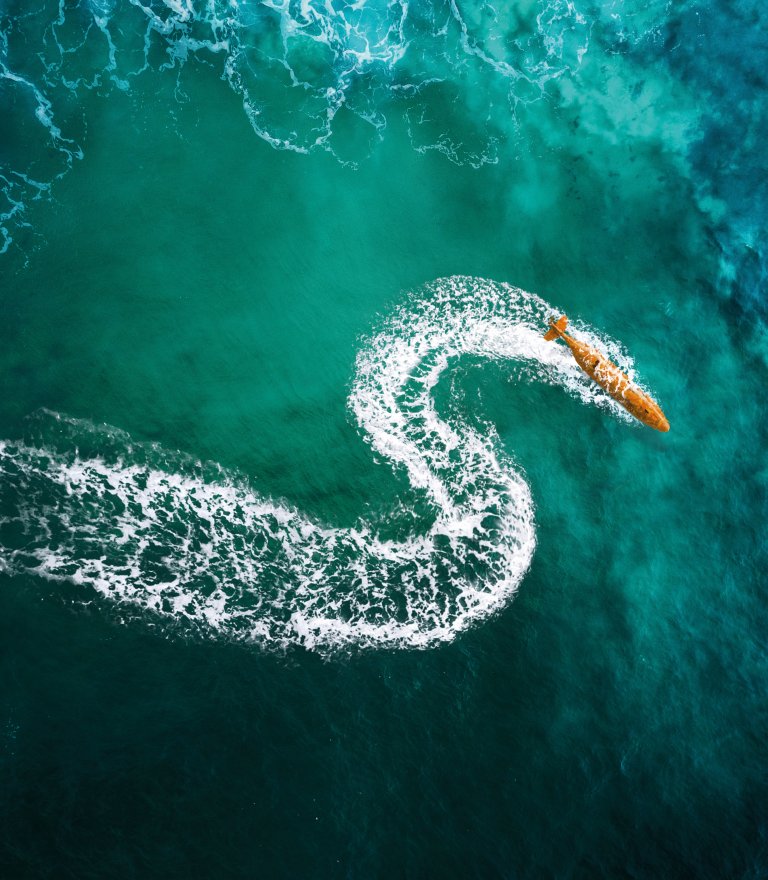